Project management is an essential part of running a business. Whether you’re working on projects for clients or have assignments that are conducted internally, without an effective project management system, you don’t have a way of tracking tasks, team members, and communication effectively. There are different types of project management systems and styles that can be used. Each comes with its own range of benefits.
Lean project management is a term that was officially coined several decades ago. It became a relatively popular method of managing projects after it was introduced by Toyota in the manufacturing space. Soon, other companies also started to use the principles behind this method to manage all sorts of projects.
Read on to learn more about what lean project management is. We’ll look at the benefits you get from this type of project management, and consider how you can start to take advantage of this strategy.
What Is Lean Project Management?
We’ll start by considering exactly what lean project management means and how it works. This will give you an idea of where such a strategy may fit into your business.
Lean project management refers to a system where a project is managed in a way that minimizes the waste experienced during every step or task. It means that you’re only using the exact amount of effort, resources, and work that is necessary to get something done. This is why the term “lean” was introduced here – as it creates a “leaner” method of managing a team, project, clients, and other internal business operations.
Why Was Lean Project Management Developed?
Lean project management was first developed back in 1950. At this time, Toyota utilized a lean methodology. While the principles of this project management method were developed in the 1950s, it was not officially coined as a term at the time.
In the 1970s, regions around the manufacturing facilities of Toyota experienced an oil crisis. By the start of 1973, oil was selling at a price of $11.65 per barrel. In just one year, the price had increased by an amount of over 400%. This created a crisis – and placed the company in a difficult position.
The Five Pillars Of Lean
At this time, Toyota decided to apply the strategies that were initially developed in 1950. These strategies included the five core values of lean, which are, as according to the Project Management Institute:
- Specify value – This means you understand what the product or service is worth in the eyes of your customer.
- Identify the value stream for each product – Value stream = the process of executing and delivering a product to a customer at the specified value. By identifying the value stream, you understand how you’re going to go from no product to an end result.
- Make value flow by eliminating waste – Ensure that the process can be completed thoroughly without spending unnecessary time, resources, or energy.
- Let the customer pull the flow – Instead of implementing a “push approach,” let customer demand determine how and when you’re producing items. This ensures that you’ll always be producing the “right” amount and not overextending yourself.
- Constant improvement in pursuit of perfection – This is self explanatory. Constantly iterate and see where you can reduce time and resources expended.
A decade later, the system was named “lean project management,” – and Toyota was not the only company to continue benefiting from the strategy. Today, many companies implement lean management strategies. This has helped to minimize resource waste and helped companies gain more value for the projects they work on.
Lean Project Management Pros and Cons
There are several advantages that come with the implementation of lean project management for your business. By recognizing these benefits, you’re able to see which apply to your specific business model. It also gives you a view of what you can expect if you decide to adopt an appropriate strategy.
Let’s take a look at the benefits companies report when they use lean project management:
- Inventory space requirements are reduced. This also helps to lower the costs associated with inventory storage.
- Quality of service and the delivered product will generally be increased.
- Lead times and completion times for project tasks are reduced.
- Many companies find that customer satisfaction improves. This is generally due to greater productivity when lean project management is used. The overall efficiency of the company’s internal operations improves too.
- From a broader viewpoint, companies tend to notice a reduction in the overall costs associated with projects and other business operations.
Lean project management was made to provide better value from every task that a business takes on. It was developed by experts, and the strategy has proven itself highly effective. With this in mind, it is quite rare to find a company that complains about the disadvantages associated with lean project management. Remember that this system gives you a guideline – it’s still up to you and the management team in your business to develop a strategy that will take advantage of this option.
Getting Started With Lean Project Management
Before implementing lean project management in your business model, it’s important to first consider if the process is appropriate. Not all businesses will be able to effectively benefit from using this type of strategy when embarking on new projects.
Consider the fundamentals and purpose of the management system. This will help guide you toward a final decision.
It’s also important to discuss the changes that will come with the use of a lean concept in the process of team management with directors and other appropriate staff. All members should be in agreement before this strategy is implemented. When some members are not on board, it may reduce the efficiency of the system or lead to problems down the line.
At this point, it’s important to consider the fundamentals that are associated with lean project management.
This starts by specifying the value that the project is able to offer. The value specifically refers to what the project offers from a client’s viewpoint. Create a visual guideline that starts at the planning phase and goes all the way to the final creation of a product or delivery of a service.
This allows you to analyze your processes – it also ensures you can identify areas where too many resources or materials are being used. In these sections, alterations can be made. See where you can minimize the use of labor and time used. If space can be saved, this opens up the opportunity for additional tasks or a more productive work environment.
Why Hive Is Ideal for Lean
When you’re implementing a lean project management methodology, using tools to help expedite and manage processes can be very helpful. To manage projects with lean, having a tool with Gantt charts and Kanban, like Hive, is your best bet. Gantt charts let you map out each task that goes into the completion of a campaign or project, and helps you understand exactly who needs to be involved.
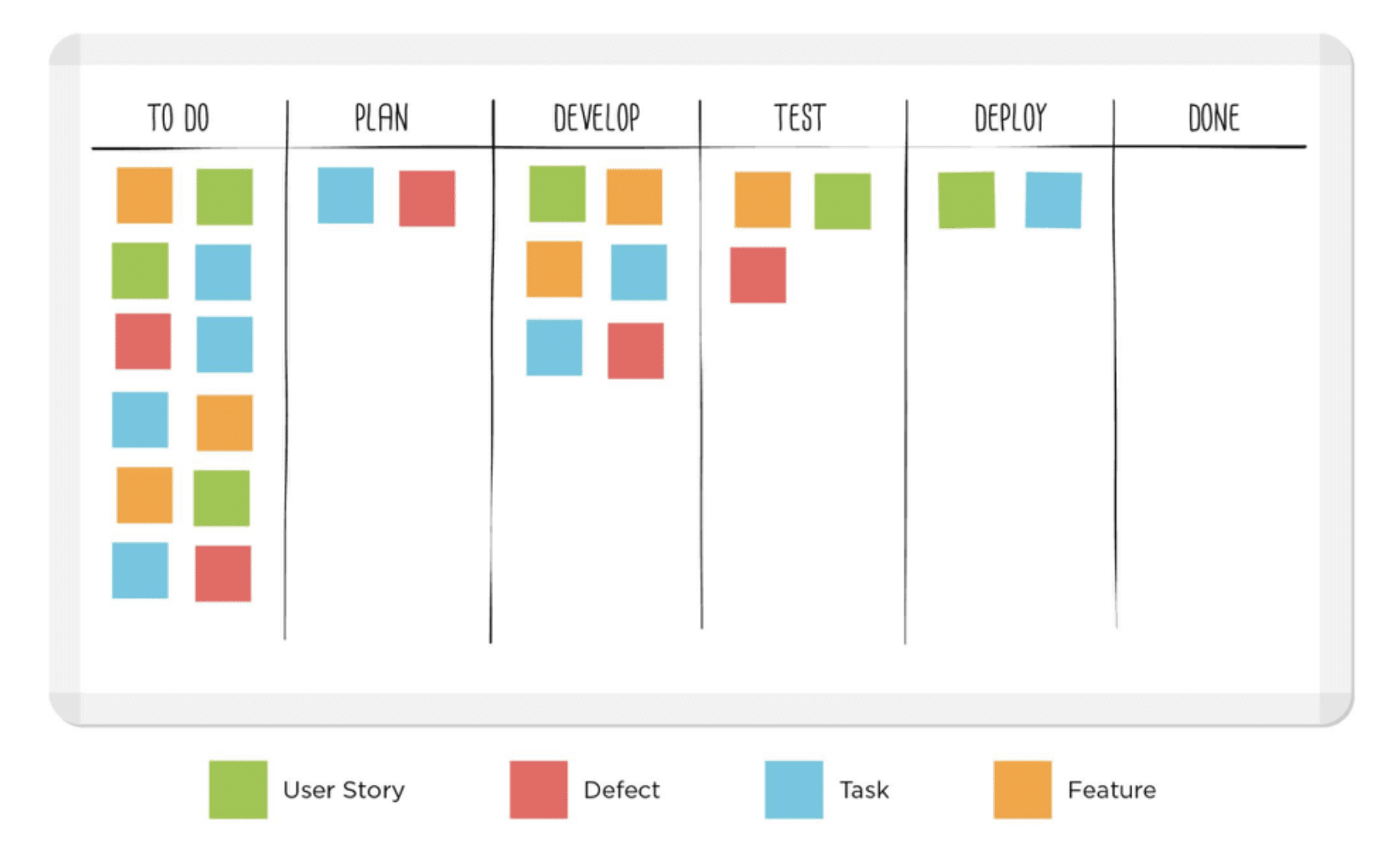
Kanban, a tool that was used at Toyota many years ago, is a system where tasks are moved into specific phases. It’s so popular among lean teams that it is even estimated that 73% of lean teams use Kanban boards. Kanban is great to utilize in lean project management because it helps you determine when tasks can move onto the next phase of the project, limiting overcrowding of tasks at a certain stage, or bottleneck.
Another aspect of Hive that is great for lean project management is the timesheets and resourcing functionality. These aspects of Hive help individuals map out exactly how much of their time is going to specific projects, and can help prevent burnout or over-exertion of resources. Additionally, Hive Analytics can give you macro-level looks at tasks completed by team, project and workspace for even more insight.
Conclusion
Managing a project with lean is an effective way of keeping track and making adjustments for improved profit and productivity. Lean project management provides a further enhancement in the value your business can gain from every project it takes on. While the implementation of a lean project management strategy may take a little effort, it’s sure to pay off in the long run.